- TOP
- Recruitment Information
- New graduate recruitment
- Quality Management(Inspection and Warranty)
Quality Management(Inspection and Warranty)
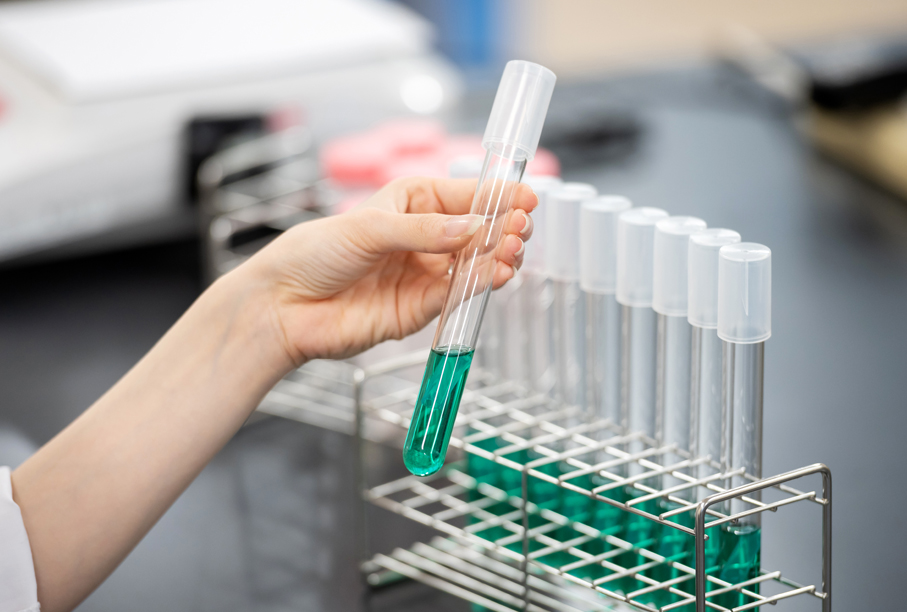
(Quality Inspection Position)
Job Description
・Microbiological testing to prove food safety (measurement of general live bacteria, coliform bacteria, fungi, etc.)
・Physical and chemical testing to prove food quality (measurement of moisture, color, grain size, etc.)
Job satisfaction and fun
・You will be able to work in quality control at a leading company with 130 years of history that exports matcha all over the world.
・You will gain expertise in safety and quality, which are considered the most important aspects of the food industry today.
・You will have your own factory and be able to inspect your own products made by colleagues you know well.
(Quality Assurance Position)
Job Description
・Inspection of matcha manufacturing factories and process improvements for quality control
・Responding to inquiries about quality and quality control from business partners
・Creating various documents for quality assurance of matcha
・Certification work: Acquisition and continuation of various certifications (FSSC22000/organic/Kosher/Halal, etc.), and audit response
*For those who prefer to use English, the following overseas assurance work is available.
・Responding to inquiries and questionnaires about quality from overseas customers
・Overseas legal affairs (researching the laws and regulations of export destination countries (pesticide residue standards, etc.)
Job satisfaction and fun
・You can acquire expertise in quality assurance and quality control, which are the lifeblood of food manufacturers.
・You can use English at work, learn expertise and improve your skills while working.
Application details
- Starting salary
- Graduate school graduate…222,000 yen / Graduate from 4 universities…211,000 yen / Junior college graduate…196,000 yen / Transportation expenses (maximum 18,000 yen)
Overtime pay will be paid in full on a minute-by-minute basis (not a fixed overtime pay).
- Salary increase
- Once a year (February)
*There is a personnel evaluation system. Salary increases are based on twice-yearly personnel evaluations and the published salary scale.
- Bonus
- Twice a year (June, December) + Year-end bonus (January)
- Location
- 33-3 Arako, Yonezu-cho, Nishio City, Aichi Prefecture
- Working hours
- 8:15~17:30
- Holidays and vacations
- 120 days per year (two days off per week, based on the company calendar)
- Employee Benefits
- Housing allowance, child allowance, position allowance, long-service merit bonus, meal allowance, full insurance (health, welfare, employment, industrial accident), company trips (optional. Fully funded by the company, travel on working days), company recreational events (cherry blossom viewing, BBQ, bowling tournament, etc.), health checkups, uniforms provided, employee discounts, paid holidays, retirement benefits, childcare leave, nursing care leave
How to apply and Selection process
- Document screening
- First interview
- Written test & Final interview
First, please apply using the button below.
Job description of Quality Management(Inspection and Warranty)
We quantify the quality and safety of food (mainly matcha) through various tests.
Tests are broadly divided into two types. Microbiological tests measure the number of general viable bacteria, coliform bacteria, fungi, etc. to prove safety.
Physicochemical tests measure moisture, color, particle size, etc. to prove quality.
We also manage AIYA's manufacturing process through regular in-house inspections.
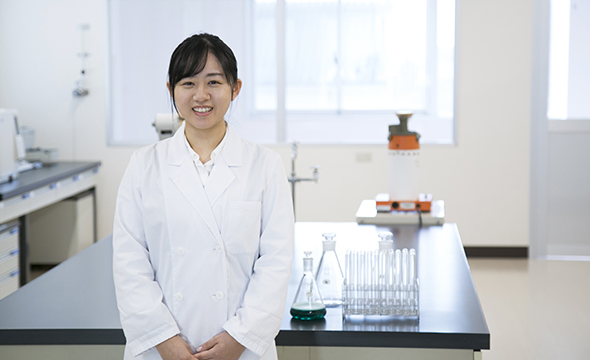
Guardian of quality Proof of quality with reliable inspection technology
InspectorTomomi Satou
Proven inspection skills provide reliable quality certification
In the food industry, quality and safety are especially important, but you can't tell these things just by looking at matcha. For that reason, it is necessary to objectively show numerical data through testing. However, if the calculated values of that data differ depending on who is testing, it's meaningless.
When you join the inspection department, you will first thoroughly hone your inspection skills. You will undergo repeated training with our education staff and take our in-house certification exam. Only after passing the exam will you be in charge of product inspection.
AIYA is a company with 130 years of history. Companies do business with us on the basis of the trust that our predecessors have built up. This department is responsible for that trust in AIYA. There is a lot of responsibility, but it is also a job that is rewarding and gives you a lot of pride.
Quality inspections will also become globalized
AIYA has local subsidiaries in the United States, Germany, Austria, China, and Thailand, and delivers matcha and other tea products all over the world. As the company globalizes, the inspectors must keep up with it. This means that they must comply with not only domestic standards and inspection methods, but also international standards and inspections. Each client also sets its own standards and may request unconventional inspections and analyses.
In addition, while AIYA's main product is matcha, they also inspect roasted green tea, rooibos tea, jasmine tea, black tea, and in some cases, the raw tea leaves before they are ground in a tea mill.
In the midst of all the changes, the inspectors are also expected to constantly take on new challenges.
Protecting AIYA's manufacturing quality
Just because we produce matcha on the same equipment as yesterday does not mean that it will be of the same quality. Of course, we also inspect the matcha before shipping, but at that stage the matcha is already completed. If it does not meet the standards, there is a risk that it will not be delivered on time, which would be a loss for the company. For this reason, our inspectors regularly sample the matcha produced each day to check its quality.
The data from these regular inspections and any changes in it allow us to inspect the manufacturing status of Aiya itself. If there is a problem, each department will work together based on the inspection report to investigate the cause and make improvements. For Aiya, which has been in business for 130 years, to continue to grow in the future, the foundation of matcha production quality is more important than anything else. Our job is to support that foundation.
Building trust through the quality and certification of AIYA products
Acquisition and management of "certification" that creates credibility for the company
The Quality Assurance Department is responsible for objectively certifying the safety and quality of AIYA's products. Product safety and quality are especially important for food manufacturers. However, trust cannot be gained by the company's claims alone. That is why it is important to obtain "certification," a proof of recognition by a third-party organization. Obtaining, maintaining, and managing certification creates objective trust for AIYA.
For example, AIYA has obtained FSSC22000 certification, which is an enhanced version of the international food safety standard ISO22000. In other words, a third-party organization has certified that AIYA's manufacturing system is safer.
AIYA exports matcha all over the world. Across different countries and cultures, objective proof is essential to gain trust. That is the role of the Quality Assurance Department.
Export support supporting AIYA's global expansion
AIYA has local subsidiaries in the United States, Germany, Austria, China, and Thailand, and delivers matcha all over the world. However, just because we have offices overseas does not mean that it is easy to deliver matcha.
Each country has its own regulations for imports, and anything that does not comply with these cannot be imported or sold. We need to research the regulations of each country, adjust our company's operations to meet them, and prepare products that can be exported. We also receive various inquiries about quality and safety from overseas business partners, so we investigate and respond carefully.
Each of these responses builds AIYA's credibility. Demand for matcha overseas is increasing year by year, and AIYA's export volume continues to increase. The work of the Quality Assurance Department supports this foundation.
Reconstructing the entire organization through authentication
AIYA has obtained many certifications, including FSSC22000 food safety certification, organic certification, Kosher food code, Halal food code, and Rainforest Alliance certification for environmental friendliness. These are not just decorations, but customer needs and the voice of the times. In addition to these, each business partner is now required to have its own ethical code, and not only the products but also the social responsibility of the company is being questioned.
In order to seriously address these voices, we must not just clear the conditions on an ad hoc basis, but reconstruct the entire organization to fit the changes of the times. AIYA has a history of 130 years, but there will be no growth without change. The work of the Quality Assurance Department is to build AIYA's credibility externally while also creating a corporate organization that is appropriate for the times from within.
Recruitment type
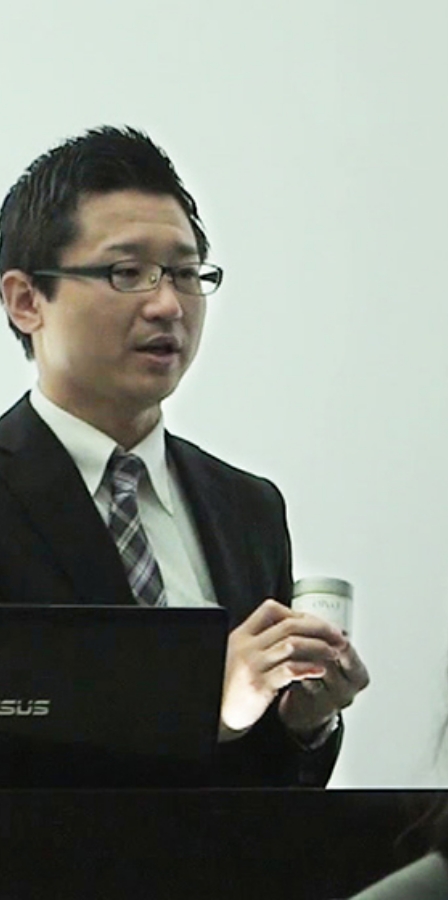
Sales JobBusiness Development Division
Proposal sales to food manufacturers, sample product creation, factory facility tours, etc.
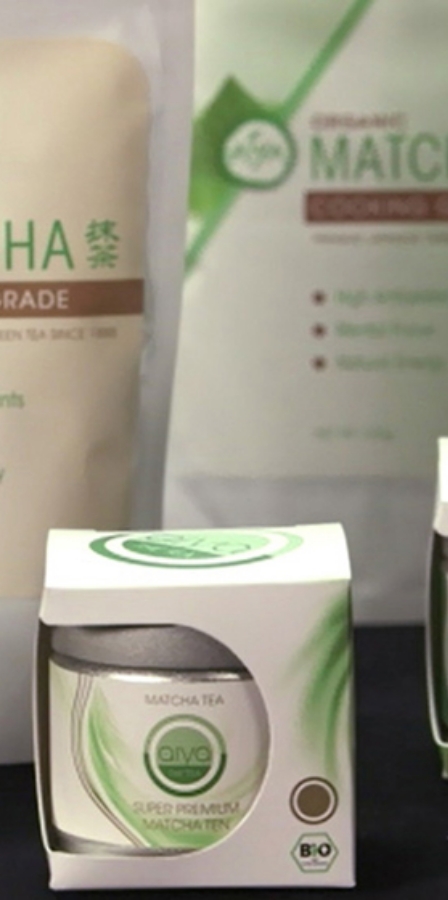
Administrative jobDomestic affairs/overseas affairs
Accepting orders, responding to inquiries, manufacturing requests, inquiries from overseas corporations, creating invoices, etc.
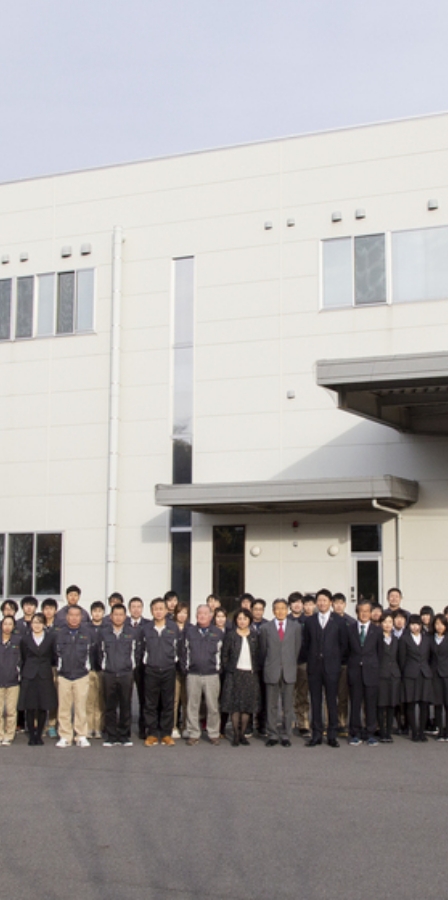
HR and General AffairsPersonnel and General Affairs Division
Employee attendance management, payroll processing and management, etc.
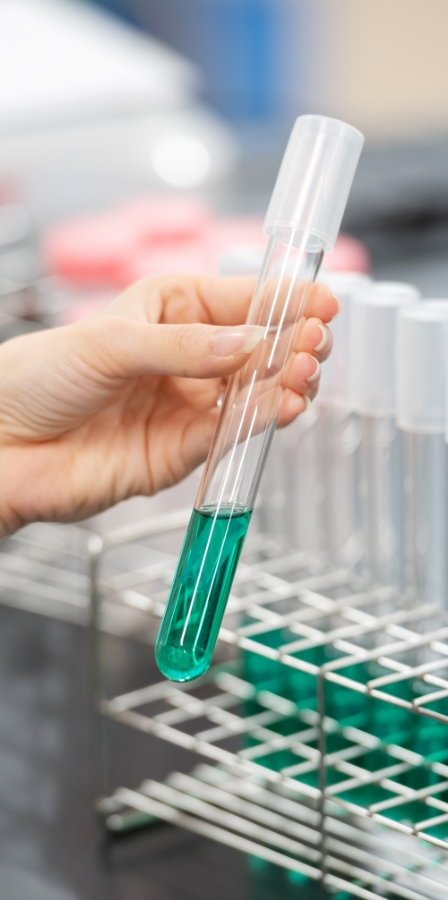
Quality ManagementInspection and Warranty
Microbiological testing, physicochemical testing, preparation of test result reports, regular inspection of factory facilities, etc.